LC-3 B - NWF
TNT Printing and Cutting Line
Machines > No Woven Fabric > LC-3 B
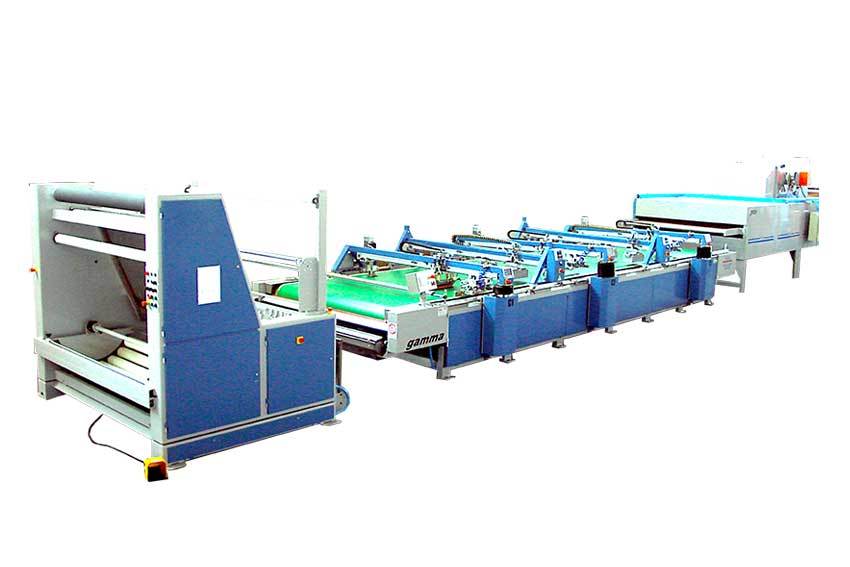
Printing line for non-woven fabric, from reel to reel, the printing line is composed as follows: introduction by reel with INT-01-NWF; printing machine equipped with 3 silk screen printing units + 2 intermediate drying hoods; Ghibly NWF drying oven; on exit the non-woven fabric is rewound using the rewinder EXT-01-NWF.
This printing line allows you to manage the printing phase automatically and independently from the other processes, cutting and sewing must be performed by other machinery.
MAIN TECHNICAL FEATURES
- TNT unwinder, possibility to manage from 1 to 2 reels at a time, the fabric after being cut down is folded to remove any tension on the fabric to be printed.
- The unwinder feed the printing line, a photocell controll the correct unwinder speed.
- The printing belt is drived by a servo motor that allow the correct printing posictioning.
- A glue layer that cover the printing belt give adesion to the fabric.
- N.3 Screen printing unit
- Stroke lenght, squeges inclination, pressure and number of passes can be adjust
- Possibility to mount frames of different sizes up to the maximum size managed by the machine.
- Print formats: 100x140 cm, 120 x160 cm, 140 x 160 cm cm, 140 x 180 cm, others on customer request
- No. 2 double intermediate drying hoods with adjustable stroke, (on customer request also adjustable power)
- Hood drying width: 40 cm (different sizes uppon request)
- machine press to apply transfer or polish plastisol (optional)
- Manageable materials: non-woven cotton or non-woven polypropylene.
- Carpet washing system (optional)
- Ghibly gas oven with three passages: this 6 mt total length oven allows to triple the residence time of the fabric in the oven, after a first passage the fabric is sent back thus giving the possibility to lower the drying temperature to 60°C and be able to dry the print effectively without rise to much the temperature in the dryer.
- EXT-01-NWF: the line ends by rewinding the reels, special laser systems allow that the reels is rewound straight.
- Total line length: 1500 cm
- Total line width: 270 cm
- Worktop height: 91 cm
- Theoretical production: 10-12 cycles / min
- Electric power installed:
- INT-01-NWF: 3 Kw
- GA-3 colors + 2 IR hoods 40x2: 29 Kw
- Ghbly Gas: 2,5 Kw + 90,000 Kcal
- EXT-01-NWF: 3 Kw
- Total: 38 Kw + 90.000 Kcal
Line Description
Structure
Made of monobloc electro-welded steel completely painted and guarded in all its parts.
A carbon sheet will be applied to the wooden panel.
A carbon sheet will be applied to the wooden panel.
Print unit
- Central structure printing unit with single linear guide.
- Squeegee speed linearly variable from 0-50 m / min.
- Pneumatic squeegee with registers for adjusting the pressure and angle of attack.
- Transversal and longitudinal centering registers of the drawing.
- Pneumatic unilateral lifting.
- Determination of the squeegee stroke independent and adjustable by magnetic switches.
- Pneumatic panel fixing with ref. side. li>
- Printing unit is equipped with a membrane keyboard to control:
- A) Manual squeegee test.
- B) Selector for raising and lowering and total panel raising.
- C) Independent adjustment of doctor blade and scraper speed.
- D) Lever for pneumatic opening / closing of the frames.
- The determination of the number of passes is programmed on the general control panel.
IR hood for intermediate drying
- Hood support trolley designed for fixing on the longitudinal guides of the machine.
- N ° 1 steel hood with radiating surface 40x140 cm each. complete with carriage for transversal movement and independent handwheel for height adjustment.
- Electrical panel for controlling and switching on the hoods with timer.
- Electric absorption 6 kW each.
- Power supply from electrical panel.
- Voltage 380 V / 3/50 Hz.
Cutter
- Electrowelded bridge structure complete with supports for fixing the cutter. Motorized linear guide having the same technical characteristics as those currently mounted on the print carriages.
- Pentoragonal Rasor motorized blade complete with wedge base.
- V-shaped wedge for invitation to start cutting
- Electrical control panel complete with inverter for cutting speed variation
- Proximity for blade stroke adjustment
- Remote control switch for synchronizing the cutter to the machine
Sheet Drag Group
Mounted on a double guide linear drive unit, it will have the
function of transporting the sheet from the gripping position to
correspondence of the blades, to its maximum length and to the intermediate measures preset by the position of the adjustable limit switch.
Gripper speed adjustment.
When loading the fabric, a roll panel will be inserted.
Gripper speed adjustment.
When loading the fabric, a roll panel will be inserted.
Stacker
The cut sheets will be superimposed keeping the upper level constant,
The raising and lowering of the pallet racking castle will be automatically controlled by photocells.
The raising and lowering of the pallet racking castle will be automatically controlled by photocells.
Endowment
Laser
Meter stops fabric (one before cutting and one at the entrance)
Meter stops fabric (one before cutting and one at the entrance)